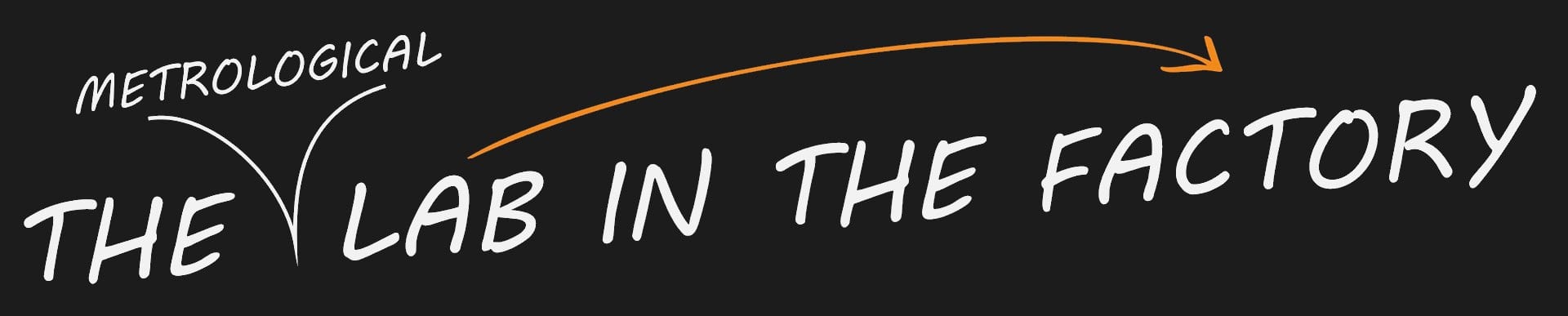
- Thermische Kompensation
- Schwingungsstabilisierung
- Echtzeit-Wiederholbarkeit und Genauigkeitsprüfung
- Digitale Schmutzentfernung
- Mikrometrische Genauigkeit
PRÄZISES MESSEN IN DER INDUSTRIE: PRÄZISION DER LABORMETROLOGIE IN DER PRODUKTIONSUMGEBUNG
Eine präzise und schnelle Messung in einer Produktionsumgebung zu erhalten, ist eine Realität der Industrie 4.0, die ein Unternehmen auf internationaler Ebene wirklich wettbewerbsfähig macht.
In den letzten Jahren wird die Qualitätskontrolle und Messung von 100% der Fertigungsproduktion zunehmend gefordert.
Für viele Industriesektoren besteht ein zunehmender Bedarf, sicherzustellen, dass alle Produkte den Spezifikationen entsprechen, was einen Wechsel von der manuellen zur automatischen Qualitätskontrolle fördert. Die Forderung nach Zuverlässigkeit des Produkts in PPM (Parts Per Million) , macht die im Labor durchgeführte statistische Stichprobenkontrolle unzureichend.
Auf der anderen Seite hat die praktische Anwendung der Metrologie immer ihre natürliche Heimat in einer kontrollierten Umgebung, dem Labor, gefunden. Die für die Durchführung von Messungen konzipierten Instrumente und Technologien haben sich an diese Umgebung angepasst. Tatsächlich führt die einfache Anpassung dieser Instrumente an die Produktionsumgebung oft zu Zuverlässigkeitsproblemen.
Das Verlassen des Labors und das direkte Betreten der Fabrik mit schnellen und zuverlässigen Kontrollen ist nur mit neuen Technologien möglich. Der Hauptzweck besteht darin, eine schnelle mikrometrische Messung in einer Produktionsumgebung, also in einer unkontrollierten Umgebung, zu erhalten.
Um dieses technologische Feld besser zu identifizieren, wurde vor kurzem der Neologismus geschaffen".Metrotronik", das Ergebnis der Vereinigung von Metro(logia) und (mecca)tronica.
Der Begriff Metrotronik entstand aus der Notwendigkeit heraus, eine Reihe von Handlungen, Gedanken, Regeln und Technologien zu identifizieren, die die Anpassung metrologischer Instrumente darstellen, damit sie direkt und effektiv in einer industriellen Produktionsumgebung arbeiten können.
"DAS METROLOGISCHE LABOR IN DER FABRIK" ist die Philosophie hinter diesem Gedanken. Man muss in der Lage sein, schnelle und automatische Messsysteme für die Industrie zu schaffen, mit der gleichen Präzision, die wir in einem Metrologielabor hätten.
Es folgt ein kurzer Vergleich, um die Gründe für die Unterschiede zwischen den Technologien im Labor und in der industriellen Umgebung besser zu verstehen.
Vorteile der Metrologie in der Produktionsumgebung: präzise Messungen in einer industriellen Umgebung, zuverlässig, schnell und wiederholbar
- misst alle Teile in einer industriellen Umgebung.
- Die automatische Messung ist in der Auswertung konstant.
- Messung in der Industrie reduziert die Anzahl der Ausschussteile aufgrund der Latenzzeit der periodischen Inspektion im Labor.
- reduziert die Zeit, die für den Aufbau von Produktionsanlagen benötigt wird.
- Messinformationen können direkt und in Echtzeit auf die Produktionsanlagen zurückdatiert werden.
- Die Messung in einer industriellen Umgebung hat eine höhere Zuverlässigkeit als Stichprobenkontrollen.
- reduziert die Kosten für mangelnde Qualität.
- Die Messung direkt in der Produktionsumgebung ermöglicht ein objektives und unmittelbares Feedback.
- Die Driftinformationen der Maßnahme sind für die vorbeugende Wartung nützlich.
- erhöht die Qualität und den Wert des Produkts
- verbessert das Unternehmensimage.
Metrologische Laborpräzision in der Produktionsumgebung
TEMPERATUR: LTC (Thermische Kompensation im Labor)
Eine der Hauptursachen für den Verlust der Messgenauigkeit in einer industriellen Umgebung ist auf die thermische Ausdehnung zurückzuführen.
Zum Beispiel hat ein Objekt aus 42 mm Aluminium einen Ausdehnungskoeffizienten von 1 Mikron für jedes Grad Celsius. Um eine korrekte Messung zu erhalten, ist es daher notwendig, die Temperatur der Instrumente, der Umgebung und jedes einzelnen zu messenden Objekts zu kennen.
Das LTC-Modul ermöglicht es, durch 4 Erfassungsstufen die gleiche Genauigkeit wie in einem Messlabor (20° ±1°) auch in Produktionsumgebungen mit einem Temperaturbereich zwischen 10° und 60° zu erreichen.
In nur 2 Hundertstelsekunden werden bis zu 4 Temperaturquellen analysiert und kompensiert.
1) die Umgebungstemperatur
2) die Temperatur des Stücks
3. die Temperatur der Spurweite in der Linie
4) die Temperatur des Messinstruments
VIBRATION: MSA (Mikrostabilisierte Genauigkeit)
Die Produktionsumgebung ist nicht frei von Vibrationen verschiedener Art, die die Messwiederholbarkeit der Instrumente erheblich beeinträchtigen.
Tatsächlich liefert ein großer Teil der heutigen Instrumentierung keine Informationen über die Zuverlässigkeit der Messung zum Zeitpunkt der Durchführung, so dass es im Falle von Vibrationen möglich ist, dass eine falsche Messung auch von korrekt kalibrierten Instrumenten erkannt wird.
Das Modul Micro Stabilized Accuracy (MSA) analysiert die Art der Schwingung und liefert einen zuverlässigen Messwert.
Der MSA-Algorithmus berechnet die Wiederholbarkeit in Echtzeit legt fest, wie messbar der Teil ist. Auf diese Weise erhalten Sie die Gewissheit, dass die Messung in der Produktionsumgebung korrekt ist, was mit anderen Instrumenten nicht möglich ist. Wird z.B. eine Situation mit schlechter Wiederholbarkeit festgestellt, kann die Messung wiederholt werden.
IPER-RESOLUTION: XVR2 (Erweiterte virtuelle Auflösung 2)
Unterauflösungstechniken ermöglichen es, die Auflösung einer Kamera zu erhöhen, indem eine Matrix von Subpixeln (in diesem Fall 8 x 8) unter Verwendung verschiedener Technologien erzeugt wird.
Durch "kontrolliertes tiefes Lernen" werden Subpixel aus der Analyse benachbarter Pixel auf der Grundlage vorab erworbener Modelle erzeugt. In der Metrologie werden besonders zuverlässige Lernmodelle verwendet, die gegengeprüft werden, um zu verhindern, dass ungenaue Informationen generiert werden, daher der Ausdruck "kontrolliert tiefes Lernen".
Eine weitere Technologie, die bei diesen Mikrometern zum Einsatz kommt, ist die "Pixelverschiebung". Die Subpixel werden durch die Analyse von aufeinanderfolgenden Bildern erzeugt, die zu unterschiedlichen Zeiten und an unterschiedlichen Positionen aufgenommen wurden.
All diese Technologien ermöglichen es uns, die bemerkenswerte Auflösung von 750 Mpixel zu erreichen.
UNTERHALB DES MIKROMETERS
Bei der optischen Messung von Objekten mit Auflösungen unterhalb des Mikrometers stoßen wir auf Probleme im Zusammenhang mit der Wellenlänge des Lichts. Einer davon ist der "Speckle"-Effekt, der durch die Beleuchtung eines Objekts mit einer monochromatischen Lichtquelle hervorgehoben wird (mit einem Laser ist der Effekt auch mit dem bloßen Auge sichtbar).
Das monochromatische Licht ist an seiner klaren roten, grünen oder blauen Farbe zu erkennen.
Es wird beobachtet, dass das durchgelassene Licht nicht verteilt ist, sondern sich aus Intensitätsspitzen auf einem dunklen Hintergrund zusammensetzt. Dieser Effekt beeinflusst die Messwiederholbarkeit noch weiter, und aus diesem Grund verwenden wir eine bestimmte gestaffelte polychromatische Beleuchtung, bei der die einzelnen Wellenlängen, aus denen sie sich zusammensetzt, nicht mehrfach sind. Das gestaffelte polychromatische Licht ist an seiner weißen Färbung zu erkennen.
Die Art des zu messenden Materials, seine Färbung und Oberflächenbeschaffenheit können kleine Ungenauigkeiten verursachen. Daraus ergibt sich die Notwendigkeit, eine Reihe von Algorithmen zu entwickeln, die in der Lage sind, diese Situation auszugleichen.
REINIGUNG: DAF (Schmutziger erweiterter Filter)
Das Auffinden sauberer Teile in der Produktionsumgebung ist keine Selbstverständlichkeit, aber für die Optimierung von Messungen in der Industrie unerlässlich. Der elektronische DAF (Dirty Advanced Filter) erlaubt es, sowohl feste als auch flüssige Fremdkörper zu erkennen.
Schmutz, der als solcher erkannt wird, wird herausgefiltert, wodurch die Messgenauigkeit verbessert wird.
Wenn die Schmutzmenge so groß ist, dass die Messung unzuverlässig ist, bewertet der Algorithmus die tatsächliche Messbarkeit des Teils, was zu einer vorbeugenden Abweichung oder einer Aufforderung zur Nachmessung nach der mechanischen Reinigung führen kann.
POSITIONIERUNGSKORREKTUR
Automatische Systeme haben nicht immer die Möglichkeit, Teile präzise zu positionieren, auch um die Handhabungszeiten zu verkürzen. Um präzise Messungen zu erhalten, ist es daher notwendig, dass das System die Achse des Teils automatisch und genau berechnet.
Die Generierung der Werkstückachsen ist konfigurierbar und ermöglicht die Anpassung aller Dimensionen. Es besteht die Möglichkeit, mehr als eine Achse zu erzeugen.
AUTO-KALIBRIERUNG
Ein Messinstrument, das ungenaue Werte liefert, ist immer ein Generator heimtückischer Probleme. Messsysteme in industriellen Umgebungen sind oft anfälliger für Änderungen der Genauigkeit.
Mit den VEA-Mikrometern können Sie eine automatische Kalibrierung durchführen oder zumindest eine fehlerhafte Kalibrierung feststellen. Es können zwei Kalibrierungsmodi gewählt werden.
Echtzeit-Autokalibrierung durch eine im Sichtfeld platzierte Referenz.
Periodische Multi-Master-Autokalibrierung (bis zu 20), bei der alle Kalibrierungsparameter an einer Reihe von Referenzmastern eingestellt werden.
Die Master können manuell oder automatisch geladen werden.
Metrologische Prüfungen
Unsere Instrumente haben sowohl im Labor als auch in einer industriellen Umgebung sehr strenge Tests durchgeführt.
Zum Vergleich haben wir die Tests mit und ohne die oben beschriebenen Kompensationssysteme durchgeführt.
6 | 6 mm | ± 0,4 μm | ± 0,05 μm | ± 0,7 μm | ± 0,13 μm |
12 | 12 mm | ± 0,6 μm | ± 0,06 μm | ± 0,9 μm | ± 0,15 μm |
18 | 18 mm | ± 0,9 μm | ± 0,08 μm | ± 1,2 μm | ± 0,16 μm |
26 | 26 mm | ± 1,2 μm | ± 0,09 μm | ± 1,5 μm | ± 0,18 μm |
36 | 36 mm | ± 1,5 μm | ± 0,11 μm | ± 1,9 μm | ± 0,20 μm |
42 | 42 mm | ± 1,8 μm | ± 0,12 μm | ± 2,2 μm | ± 0,21 μm |
48 | 48 mm | ± 2,0 μm | ± 0,13 μm | ± 2,4 μm | ± 0,22 μm |
56 | 56 mm | ± 2,3 μm | ± 0,15 μm | ± 2,7 μm | ± 0,24 μm |
64 | 64 mm | ± 2,6 μm | ± 0,17 μm | ± 3,1 μm | ± 0,26 μm |
72 | 72 mm | ± 2,9 μm | ± 0,2 μm | ± 3,4 μm | ± 0,3 μm |
80 | 80 mm | ± 3,2 μm | ± 0,2 μm | ± 3,7 μm | ± 0,3 μm |
90 | 90 mm | ± 3,5 μm | ± 0,2 μm | ± 4,2 μm | ± 0,3 μm |
100 | 100 mm | ± 3,9 μm | ± 0,2 μm | ± 4,6 μm | ± 0,3 μm |
110 | 110 mm | ± 4,3 μm | ± 0,3 μm | ± 5,0 μm | ± 0,4 μm |
120 | 120 mm | ± 4,6 μm | ± 0,3 μm | ± 5,4 μm | ± 0,4 μm |
136 | 136 mm | ± 5,2 μm | ± 0,3 μm | ± 6,1 μm | ± 0,4 μm |
150 | 150 mm | ± 5,8 μm | ± 0,3 μm | ± 6,7 μm | ± 0,4 μm |
170 | 170 mm | ± 6,5 μm | ± 0,4 μm | ± 7,5 μm | ± 0,5 μm |
190 | 190 mm | ± 7,2 μm | ± 0,4 μm | ± 8,3 μm | ± 0,5 μm |
216 | 216 mm | ± 8,2 μm | ± 0,5 μm | ± 9,4 μm | ± 0,6 μm |
240 | 240 mm | ± 9,1 μm | ± 0,5 μm | ± 10,4 μm | ± 0,6 μm |
268 | 268 mm | ± 10,1 μm | ± 0,6 μm | ± 11,6 μm | ± 0,7 μm |
300 | 300 mm | ± 11,3 μm | ± 0,6 μm | ± 12,9 μm | ± 0,8 μm |
(1) Messwert mit Glaskalibrierungsskala mit 25 ±2σ Messungen
(2) Messwert mit kalibriertem Stecker der Größenklasse 1 von 60% bis 70% des Sichtfeldes mit 25 Messungen ±2σ
VIDEO-GALERIE
Spezifikationen können ohne Vorankündigung geändert werden