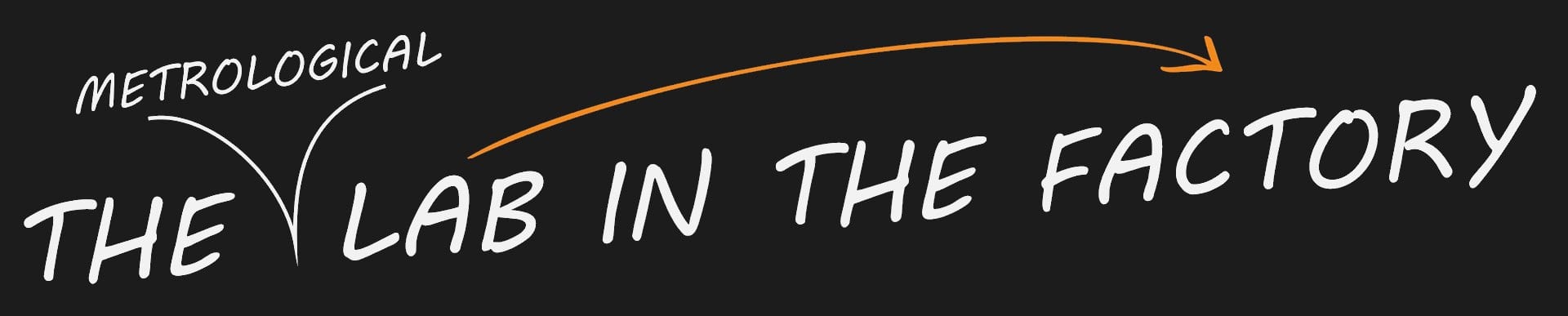
- Compensación térmica
- Estabilización de la vibración
- Comprobación de repetibilidad y precisión en tiempo real
- Eliminación de la suciedad digital
- Precisión micrométrica
LA MEDICIÓN PRECISA EN LA INDUSTRIA: LA PRECISIÓN DE LA METROLOGÍA DE LABORATORIO EN EL ENTORNO DE PRODUCCIÓN
Obtener una medición precisa y rápida en un entorno de producción es una realidad de la industria 4.0 que hace que una empresa sea realmente competitiva a nivel internacional.
En los últimos años, el control de calidad y la medición de 100% de la producción manufacturera son cada vez más necesarios.
En muchos sectores industriales existe una necesidad cada vez mayor de garantizar que todos los productos cumplan las especificaciones, lo que fomenta la migración del control de calidad manual al automático. La exigencia de fiabilidad del producto en PPM (Partes por millón) , hace que el control estadístico de la muestra realizado en el laboratorio sea insuficiente.
Por otra parte, la aplicación práctica de la metrología siempre ha encontrado su hogar natural en un ambiente controlado, el laboratorio. La instrumentación y las tecnologías diseñadas para realizar las mediciones se han adaptado a este entorno, de hecho, la simple adaptación de estos instrumentos al entorno de producción suele generar problemas de fiabilidad.
Salir del laboratorio y entrar directamente en la fábrica con controles rápidos y fiables sólo es posible con las nuevas tecnologías. El propósito principal es obtener una medición micrométrica rápida en un entorno de producción, por lo tanto en un entorno no controlado.
Para identificar mejor este campo tecnológico, se ha creado recientemente el neologismo".Metrotronics", el resultado de la unión de metro(logia) y (meca)tronica.
El término Metrotronics nació de la necesidad de identificar una serie de acciones, pensamientos, reglas y tecnologías que representan la adaptación de los instrumentos metrológicos para que puedan operar directa y eficazmente en un entorno de producción industrial.
"EL LABORATORIO METROLÓGICO EN LA FÁBRICA" es la filosofía detrás de este pensamiento. Es necesario poder crear sistemas de medición rápidos y automáticos para la industria, con la misma precisión que tendríamos en un laboratorio de metrología.
A continuación se hace una breve comparación para comprender mejor las razones de la diferencia de tecnologías en el laboratorio y en el entorno industrial.
Ventajas de la metrología en el entorno de producción: medición precisa en un entorno industrial, fiable, rápida y repetible
- mide todas las partes en un entorno industrial.
- La medición automática es constante en la evaluación.
- La medición en la industria reduce el número de rechazos debido al tiempo de latencia de la inspección periódica en el laboratorio.
- reduce el tiempo necesario para establecer las instalaciones de producción.
- La información de las mediciones puede ser retrocedida directamente y en tiempo real a las instalaciones de producción.
- La medición en un entorno industrial tiene una mayor fiabilidad que la verificación puntual.
- reduce el costo de la falta de calidad.
- La medición directa en el entorno de producción permite una retroalimentación objetiva e inmediata.
- La información sobre la deriva de la medida es útil para el mantenimiento preventivo.
- aumenta la calidad y el valor del producto
- mejora la imagen corporativa.
La precisión del laboratorio metrológico en el entorno de producción
TEMPERATURA: LTC (Compensación Térmica de Laboratorio)
Una de las principales causas de la pérdida de precisión de las mediciones en un entorno industrial se debe a la expansión térmica.
Por ejemplo, un objeto de aluminio de 42 mm tiene un coeficiente de expansión de 1 micrón por cada grado centígrado, por lo que para obtener una medición correcta es necesario conocer la temperatura de la instrumentación, del entorno y de cada uno de los objetos a medir.
El módulo LTC, permite obtener la misma precisión que se tendría en un laboratorio de metrología (20° ±1°) incluso en entornos de producción con un rango de temperatura entre 10° y 60° mediante 4 etapas de detección.
En sólo 2 centésimas de segundo se analizan y compensan hasta 4 fuentes de temperatura.
1) la temperatura ambiente
2) la temperatura de la pieza
3. la temperatura del indicador en línea
4) la temperatura del instrumento de medición
VIBRACIÓN: MSA (Precisión micro estabilizada)
El entorno de producción no está libre de vibraciones de diversos tipos y éstas afectan significativamente a la repetibilidad de las mediciones de los instrumentos.
De hecho, gran parte de la instrumentación actual no proporciona información sobre la fiabilidad de la medición en el momento en que se realiza, por lo que en caso de vibración es posible que una medición incorrecta sea detectada incluso por instrumentos que estén correctamente calibrados.
El módulo de precisión micro estabilizada (MSA) analiza el tipo de vibración y proporciona un valor de medición fiable.
El algoritmo MSA que calcula el la repetibilidad en tiempo real establece cuán mensurable es la parte. De esta manera se obtiene la confianza de que la medición es correcta en el entorno de producción, lo cual es imposible con otros instrumentos. Si se detecta una situación de mala repetibilidad, por ejemplo, la medición puede repetirse.
IPER-RESOLUCIÓN: XVR2 (Resolución Virtual Extendida 2)
Las técnicas de subresolución permiten aumentar la resolución de una cámara, generando una matriz de subpíxeles (en este caso de 8 x 8) utilizando diferentes tecnologías.
A través del "aprendizaje profundo controlado" se generan subpíxeles a partir del análisis de los píxeles adyacentes basado en modelos preadquiridos. En metrología se utilizan modelos de aprendizaje especialmente fiables, que se comprueban para evitar que se genere información inexacta, de ahí la expresión "controlado aprendizaje profundo".
Otra tecnología que se utiliza en estos micrómetros es el "pixel shifting", los subpíxeles son generados por el análisis de imágenes secuenciales tomadas en diferentes momentos y posiciones.
Todas estas tecnologías nos permiten alcanzar la notable resolución de 750 Mpixel.
POR DEBAJO DEL MICRÓN
Cuando se miden ópticamente objetos con resoluciones por debajo del micrón, nos encontramos con problemas relacionados con la longitud de onda de la luz. Uno de ellos es el efecto "speckle" que se pone de relieve al iluminar un objeto con una fuente de luz monocromática (con un láser el efecto también es evidente a simple vista).
La luz monocromática puede reconocerse por su claro color rojo, verde o azul.
Se observa que la luz transmitida no se distribuye, sino que está compuesta por picos de intensidad sobre un fondo oscuro. Este efecto influye aún más en la repetibilidad de la medición y es por esta razón que utilizamos una iluminación policromática escalonada particular en la que las longitudes de onda únicas de las que está compuesta no son múltiples. La luz policromática escalonada puede reconocerse por su coloración blanca.
El tipo de material a medir, su coloración y el acabado de la superficie pueden generar pequeñas inexactitudes. De ahí la necesidad de crear una serie de algoritmos capaces de compensar esta situación.
LIMPIEZA: DAF (Dirty Advanced Filter)
Encontrar piezas limpias en el entorno de producción no es una conclusión previsible, pero es esencial para optimizar la medición en la industria. El DAF (Dirty Advanced Filter) electrónico permite detectar la presencia de cuerpos extraños tanto sólidos como líquidos.
La suciedad que se reconoce como tal se filtra, mejorando la precisión de la medición.
Si la cantidad de suciedad es tal que la medición no es fiable, el algoritmo evalúa la mensurabilidad real de la pieza, lo que puede generar una desviación preventiva o una solicitud de medición posterior después de la limpieza mecánica.
CORRECCIÓN DEL POSICIONAMIENTO
Los sistemas automáticos no siempre tienen la posibilidad de posicionar las piezas con precisión, también para reducir los tiempos de manipulación, por lo que para obtener mediciones precisas es necesario que el sistema calcule el eje de la pieza de forma automática y precisa.
La generación del eje de la pieza es configurable y permite que todas las dimensiones se adapten. Existe la posibilidad de generar más de un eje.
AUTO-CALIBRACIÓN
Un instrumento de medición que proporciona valores inexactos es siempre un generador de problemas insidiosos. Los sistemas de medición en entornos industriales suelen ser más susceptibles a los cambios de precisión.
Los micrómetros VEA le permiten realizar una calibración automática o al menos notar una calibración incorrecta. Se pueden elegir dos modos de calibración.
Calibración automática en tiempo real por referencia colocada en el campo de visión.
Calibración automática periódica de múltiples maestros (hasta 20) en la que todos los parámetros de calibración se ajustan en una serie de maestros de referencia.
Los maestros pueden ser cargados manual o automáticamente.
Las pruebas metrológicas
Nuestros instrumentos han realizado pruebas muy estrictas tanto en el laboratorio como en un entorno industrial.
Como comparación hemos realizado las pruebas incluyendo y excluyendo los sistemas de compensación descritos anteriormente.
6 | 6 mm | ± 0,4 μm | ± 0,05 μm | ± 0,7 μm | ± 0,13 μm |
12 | 12 mm | ± 0,6 μm | ± 0,06 μm | ± 0,9 μm | ± 0,15 μm |
18 | 18 mm | ± 0,9 μm | ± 0,08 μm | ± 1,2 μm | ± 0,16 μm |
26 | 26 mm | ± 1,2 μm | ± 0,09 μm | ± 1,5 μm | ± 0,18 μm |
36 | 36 mm | ± 1,5 μm | ± 0,11 μm | ± 1,9 μm | ± 0,20 μm |
42 | 42 mm | ± 1,8 μm | ± 0,12 μm | ± 2,2 μm | ± 0,21 μm |
48 | 48 mm | ± 2,0 μm | ± 0,13 μm | ± 2,4 μm | ± 0,22 μm |
56 | 56 mm | ± 2,3 μm | ± 0,15 μm | ± 2,7 μm | ± 0,24 μm |
64 | 64 mm | ± 2,6 μm | ± 0,17 μm | ± 3,1 μm | ± 0,26 μm |
72 | 72 mm | ± 2,9 μm | ± 0,2 μm | ± 3,4 μm | ± 0,3 μm |
80 | 80 mm | ± 3,2 μm | ± 0,2 μm | ± 3,7 μm | ± 0,3 μm |
90 | 90 mm | ± 3,5 μm | ± 0,2 μm | ± 4,2 μm | ± 0,3 μm |
100 | 100 mm | ± 3,9 μm | ± 0,2 μm | ± 4,6 μm | ± 0,3 μm |
110 | 110 mm | ± 4,3 μm | ± 0,3 μm | ± 5,0 μm | ± 0,4 μm |
120 | 120 mm | ± 4,6 μm | ± 0,3 μm | ± 5,4 μm | ± 0,4 μm |
136 | 136 mm | ± 5,2 μm | ± 0,3 μm | ± 6,1 μm | ± 0,4 μm |
150 | 150 mm | ± 5,8 μm | ± 0,3 μm | ± 6,7 μm | ± 0,4 μm |
170 | 170 mm | ± 6,5 μm | ± 0,4 μm | ± 7,5 μm | ± 0,5 μm |
190 | 190 mm | ± 7,2 μm | ± 0,4 μm | ± 8,3 μm | ± 0,5 μm |
216 | 216 mm | ± 8,2 μm | ± 0,5 μm | ± 9,4 μm | ± 0,6 μm |
240 | 240 mm | ± 9,1 μm | ± 0,5 μm | ± 10,4 μm | ± 0,6 μm |
268 | 268 mm | ± 10,1 μm | ± 0,6 μm | ± 11,6 μm | ± 0,7 μm |
300 | 300 mm | ± 11,3 μm | ± 0,6 μm | ± 12,9 μm | ± 0,8 μm |
(1) valor medido con escala de calibración de vidrio con 25 ±2σ mediciones
(2) valor medido con enchufe calibrado clase 1 de 60% a 70% del campo de visión con 25 mediciones ±2σ
GALERÍA DE VÍDEOS
las especificaciones pueden cambiar sin previo aviso