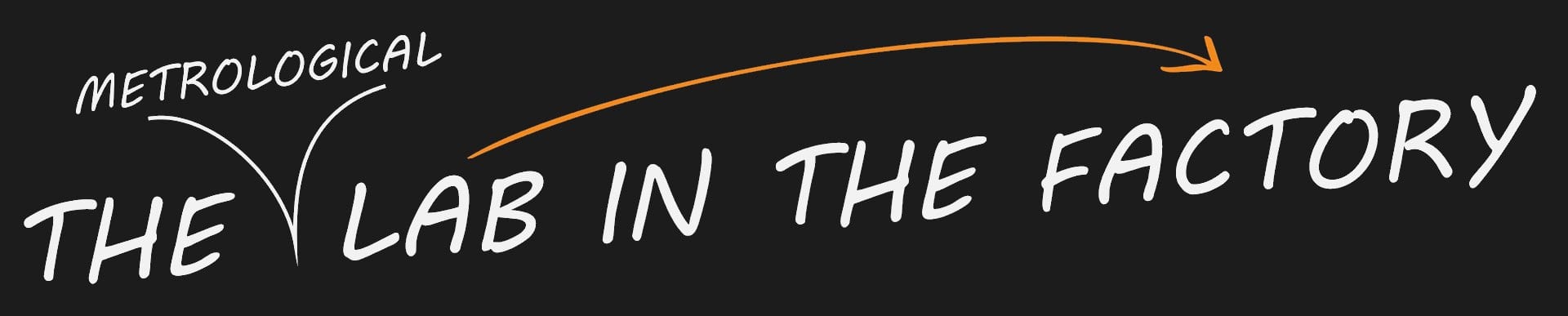
- Compensazione termica
- Stabilizzazione delle vibrazioni
- Controllo ripetibilità e accuratezza in tempo reale
- Rimozione digitale dello sporco
- Precisione micrometrica
MISURA PRECISA IN INDUSTRIA: PRECISIONE DA LABORATORIO METROLOGICO, IN AMBIENTE DI PRODUZIONE
Ottenere una misura precisa e veloce in ambiente produttivo è una realtà dell’industria 4.0 che rende realmente competitiva un’azienda a livello internazionale.
In questi ultimi anni è sempre più richiesto il controllo qualità e la misurazione del 100% della produzione manifatturiera.
Per molti settori industriali è sempre più pressante l’esigenza di garantire che la totalità dei prodotti sia conforme alle specifiche, favorendo una migrazione dal controllo qualità manuale a quello automatico. La richiesta di affidabilità del prodotto in PPM (Parti Per Milione) , rende insufficiente il controllo statistico a campione effettuato in laboratorio.
D’altronde l’applicazione pratica della metrologia ha da sempre trovato la sua sede naturale in un ambiente controllato, il laboratorio. La strumentazione e le tecnologie studiate per eseguire le misure si sono adattate a quest’ambiente, infatti il semplice adattamento di questi strumenti per l’ambiente di produzione genera spesso problemi di affidabilità.
Uscire dal laboratorio ed entrare direttamente in fabbrica con controlli veloci ed affidabili è possibile solo utilizzando nuove tecnologie. Lo scopo principale è quello di ottenere una misura micrometrica veloce in ambiente di produzione, quindi in ambiente non controllato.
Per meglio identificare quest’ambito tecnologico, è stato recentemente creato il neologismo “metrotronica”, risultato dell’unione di metro(logia) e (mecca)tronica.
Il termine metrotronica nasce dall’esigenza di identificare una serie di azioni, pensieri, regole e tecnologie che rappresentano l’adattamento degli strumenti metrologici in modo che possano operare direttamente ed efficacemente in un ambiente di produzione industriale.
“THE METROLOGICAL LAB IN THE FACTORY” è la filosofia che sta alla base di questo pensiero. E’ necessario riuscire a creare sistemi di misura per l’industria veloci ed automatici, con la stessa precisione che avremmo in un laboratorio metrologico.
Di seguito un breve confronto per meglio comprendere i motivi della differenzazione delle tecnologie in laboratorio ed in ambiente industriale
Vantaggi della metrologia in ambiente di produzione: misura precisa in ambiente industriale, affidabile, veloce e ripetibile
- misura la totalità dei pezzi in ambiente industriale.
- la misura automatica è costante nella valutazione.
- la misura in industria riduce il numero di scarti dovuti dai tempi di latenza del controllo periodico in laboratorio.
- riduce i tempi di messa a punto degli impianti di produzione.
- le informazioni di misura possono essere retroazionate direttamente ed in tempo reale sugli impianti di produzione.
- la misura in ambiente industriale ha un’ affidabilità superiore rispetto al controllo a campione.
- riduce i costi di mancata qualità.
- misurare direttamente in ambiente produttivo permette un riscontro oggettivo ed immediato.
- le informazioni sulla deriva della misura sono utili per la manutenzione preventiva.
- incrementa la qualità ed il valore del prodotto
- valorizza l’immagine aziendale.
Precisione da laboratorio metrologico, in ambiente di produzione
TEMPERATURA: LTC (Laboratory Thermal Compensation)
Una delle cause principali di perdita di accuratezza nella misura in ambiente industriale è dovuta dalla dilatazione termica.
Per esempio un oggetto di 42 mm di alluminio ha un coefficiente di dilatazione di 1 micron per ogni grado centigrado, quindi per ottenere una misura corretta è necessario conoscere la temperatura della strumentazione, dell’ambiente e di ogni singolo oggetto da misurare.
Il modulo LTC, permette di ottenere la stessa accuratezza che si avrebbe in un laboratorio metrologico (20° ±1°) anche in ambienti di produzione con range di temperature tra 10° e 60° per mezzo di 4 stadi di rilevazione.
In soli 2 centesimi di secondo vengono analizzate e compensate fino a 4 sorgenti di temperatura.
1) la temperatura ambiente
2) la temperatura del pezzo
3) la temperatura del calibro in linea
4) la temperatura dello strumento di misura
VIBRAZIONE: MSA (Micro Stabilized Accuracy)
L’ambiente di produzione non è esente da vibrazioni di varia natura e queste influiscono sulla ripetibilità di misura degli strumenti in modo significativo.
Infatti buona parte della strumentazione odierna non fornisce informazioni sull’affidabilità della misura nell’istante in cui viene eseguita, quindi in caso di vibrazione è possibile che venga rilevata una misura errata anche da apparecchi che risultano correttamente calibrati.
Il modulo MSA (Micro Stabilized Accuracy) analizzando la tipologia di vibrazione riesce a fornire un valore di misura affidabile.
L’algoritmo MSA calcolando la ripetibilità in tempo reale stabilisce quanto è misurabile del pezzo. In questo modo si ottiene quella sicurezza della correttezza della misura in ambiente di produzione, impossibile con altri strumenti. Nel caso in cui venga rilavata una situazione di scarsa ripetibilità si può ad esempio ripetere la misura.
IPER-RISOLUZIONE: XVR2 (Extended Virtual Resolution 2)
Le tecniche di sub-risoluzione permettono di incrementare la risoluzione di una telecamera, generando una matrice di subpixel (in questo caso 8 x 8) usando diverse tecnologie.
Tramite il “controlled deep learning” vengono generati dei subpixel dall’analisi dei pixel adiacenti basandosi su modelli preacquisiti. In metrologia vengono utilizzati modelli di apprendimento particolarmente affidabili, controllati in maniera incrociata per evitare che vengano generate informazioni inesatte, da qui l’espressione “controlled deep learning”.
Un’altra tecnologia che viene utilizzata in questi micrometri è il “pixel shifting“, i subpixel vengono generati dall’analisi di immagini sequenziali prese in tempi e posizioni diverse.
Tutte queste tecnologie ci permettono di ottenere la notevole risoluzione di 750 Mpixel.
SOTTO IL MICRON
Nel misurare otticamente oggetti con risoluzioni al di sotto del micron ci si imbatte in problematiche legate alla lunghezza d’onda della luce. Una di queste è l’effetto “speckle” che si evidenzia illuminando con una sorgente di luce monocromatica un oggetto (con un laser l’effetto è evidente anche ad occhio nudo).
La luce monocromatica si riconosce per la netta colorazione rossa, verde o blu.
Si osserva che la luce trasmessa non è distribuita, ma è composta da picchi di intensità su di uno sfondo scuro. Quest’effetto influenza ulteriormente la ripetibilità di misura ed è per questa ragione che utilizziamo una particolare illuminazione policromatica sfasata dove le singole lunghezze d’onda di cui è composta non sono multipli. La luce policromatica sfasata si riconosce per la colorazione bianca.
La tipologia del materiale da misurare, la sua colorazione e la sua finitura superficiale, possono generare piccole imprecisioni. Da qui la necessità di creare una serie di algoritmi capaci di compensare questa situazione.
PULIZIA: DAF (Dirty Advanced Filter)
Trovare pezzi puliti in ambiente di produzione non è un fatto scontato, ma fondamentale per ottimizzare la misura in industria. Il filtro elettronico DAF (Dirty Advanced Filter) permette di riconoscere la presenza di corpi estranei sia solidi che liquidi.
Lo sporco riconosciuto come tale viene filtrato migliorando la precisione della misura.
Se l’entità dello sporco è tale da rendere la misura non attendibile, l’algoritmo valuta l’effettiva misurabilità del pezzo che può generare uno scarto preventivo o una richiesta di successiva misurazione dopo una pulizia meccanica.
CORREZIONE DEL POSIZIONAMENTO
I sistemi automatici non hanno sempre la possibilità di posizionare i pezzi in modo preciso, anche per ridurre i tempi di manipolazione, per cui, per ottenere misure precise è necessario che il sistema calcoli in modo automatico e preciso l’asse del pezzo.
La generazione dell’asse del pezzo è configurabile e permette a tutte le quote di adattarsi. Esiste la possibilità di generare più di un asse.
AUTOCALIBRAZIONE
Uno strumento di misura che fornisce valori non precisi è sempre generatore di problematiche insidiose. Spesso i sistemi di misura collocati in ambiente industriale sono più suscettibili a variazioni di precisione.
I micrometri VEA permettono di eseguire la calibrazione automatica o quantomeno accorgersi di una non corretta calibrazione. Si possono scegliere due modalità di calibrazione.
Autocalibrazione real-time tramite riferimento collocato nel campo visivo.
Autocalibrazione periodica multi-master (fino a 20) nella quale tutti i parametri di calibrazione vengono regolati su una serie di master di riferimento.
I master possono essere caricati manualmente o in modo automatico.
Test metrologici
I nostri strumenti hanno eseguito test molto severi sia in laboratorio, sia in ambiente industriale.
Come termine di paragone abbiamo eseguito i test includendo ed escludendo i sistemi di compensazione descritti sopra.
6 | 6 mm | ± 0,4 μm | ± 0,05 μm | ± 0,7 μm | ± 0,13 μm |
12 | 12 mm | ± 0,6 μm | ± 0,06 μm | ± 0,9 μm | ± 0,15 μm |
18 | 18 mm | ± 0,9 μm | ± 0,08 μm | ± 1,2 μm | ± 0,16 μm |
26 | 26 mm | ± 1,2 μm | ± 0,09 μm | ± 1,5 μm | ± 0,18 μm |
36 | 36 mm | ± 1,5 μm | ± 0,11 μm | ± 1,9 μm | ± 0,20 μm |
42 | 42 mm | ± 1,8 μm | ± 0,12 μm | ± 2,2 μm | ± 0,21 μm |
48 | 48 mm | ± 2,0 μm | ± 0,13 μm | ± 2,4 μm | ± 0,22 μm |
56 | 56 mm | ± 2,3 μm | ± 0,15 μm | ± 2,7 μm | ± 0,24 μm |
64 | 64 mm | ± 2,6 μm | ± 0,17 μm | ± 3,1 μm | ± 0,26 μm |
72 | 72 mm | ± 2,9 μm | ± 0,2 μm | ± 3,4 μm | ± 0,3 μm |
80 | 80 mm | ± 3,2 μm | ± 0,2 μm | ± 3,7 μm | ± 0,3 μm |
90 | 90 mm | ± 3,5 μm | ± 0,2 μm | ± 4,2 μm | ± 0,3 μm |
100 | 100 mm | ± 3,9 μm | ± 0,2 μm | ± 4,6 μm | ± 0,3 μm |
110 | 110 mm | ± 4,3 μm | ± 0,3 μm | ± 5,0 μm | ± 0,4 μm |
120 | 120 mm | ± 4,6 μm | ± 0,3 μm | ± 5,4 μm | ± 0,4 μm |
136 | 136 mm | ± 5,2 μm | ± 0,3 μm | ± 6,1 μm | ± 0,4 μm |
150 | 150 mm | ± 5,8 μm | ± 0,3 μm | ± 6,7 μm | ± 0,4 μm |
170 | 170 mm | ± 6,5 μm | ± 0,4 μm | ± 7,5 μm | ± 0,5 μm |
190 | 190 mm | ± 7,2 μm | ± 0,4 μm | ± 8,3 μm | ± 0,5 μm |
216 | 216 mm | ± 8,2 μm | ± 0,5 μm | ± 9,4 μm | ± 0,6 μm |
240 | 240 mm | ± 9,1 μm | ± 0,5 μm | ± 10,4 μm | ± 0,6 μm |
268 | 268 mm | ± 10,1 μm | ± 0,6 μm | ± 11,6 μm | ± 0,7 μm |
300 | 300 mm | ± 11,3 μm | ± 0,6 μm | ± 12,9 μm | ± 0,8 μm |
(1) valore misurato con scala di calibrazione in vetro con 25 rilevazioni ±2σ
(2) valore misurato con spina calibrata classe 1 di dimensioni dal 60% al 70% del campo di visione con 25 rilevazioni ±2σ
GALLERIA VIDEO
le caratteristiche tecniche possono cambiare senza preavviso