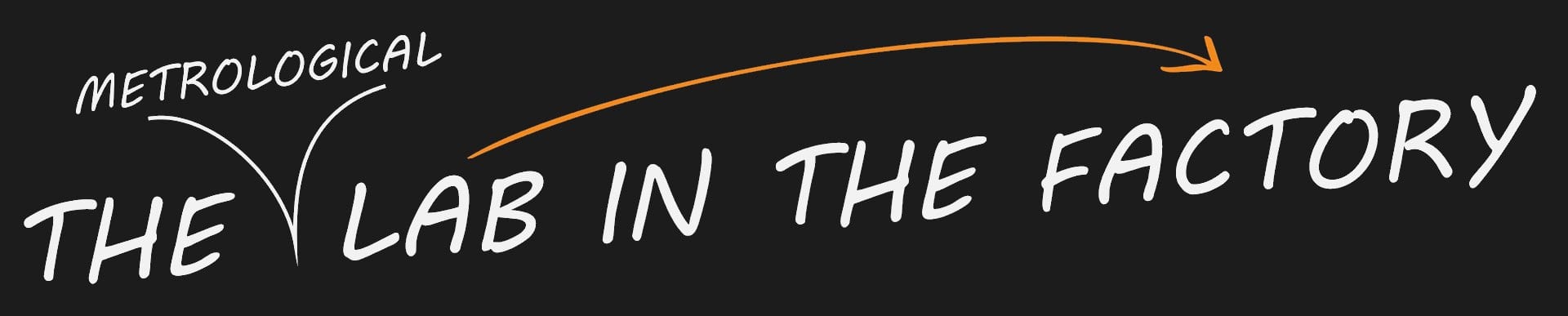
- Compensation thermique
- Stabilisation des vibrations
- Contrôle de la répétabilité et de la précision en temps réel
- Le nettoyage numérique de la saleté
- Précision micrométrique
LA MESURE PRÉCISE DANS L'INDUSTRIE : LA PRÉCISION DE LA MÉTROLOGIE DE LABORATOIRE DANS L'ENVIRONNEMENT DE PRODUCTION
L'obtention d'une mesure précise et rapide dans un environnement de production est une réalité de l'industrie 4.0 qui rend une entreprise vraiment compétitive au niveau international.
Ces dernières années, le contrôle de la qualité et la mesure de 100% de la production manufacturière sont de plus en plus nécessaires.
Pour de nombreux secteurs industriels, il est de plus en plus nécessaire de s'assurer que tous les produits sont conformes aux spécifications, ce qui encourage le passage d'un contrôle de qualité manuel à un contrôle automatique. La demande de fiabilité du produit en PPM (parties par million) rend le contrôle statistique des échantillons effectué en laboratoire insuffisant.
D'autre part, l'application pratique de la métrologie a toujours trouvé sa place naturelle dans un environnement contrôlé, le laboratoire. Les instruments et les technologies conçus pour effectuer des mesures se sont adaptés à cet environnement, en fait la simple adaptation de ces instruments à l'environnement de production génère souvent des problèmes de fiabilité.
Sortir du laboratoire et entrer directement dans l'usine avec des contrôles rapides et fiables n'est possible qu'avec les nouvelles technologies. L'objectif principal est d'obtenir une mesure micrométrique rapide dans un environnement de production, donc dans un environnement non contrôlé.
Pour mieux identifier ce domaine technologique, le néologisme a été créé récemment".Metrotronics", résultat de l'union de metro(logia) et (mecca)tronica.
Le terme Metrotronics est née de la nécessité d'identifier une série d'actions, de réflexions, de règles et de technologies qui représentent l'adaptation des instruments métrologiques afin qu'ils puissent fonctionner directement et efficacement dans un environnement de production industrielle.
"LE LABORATOIRE MÉTROLOGIQUE DANS L'USINE" est la philosophie qui sous-tend cette pensée. Il est nécessaire de pouvoir créer des systèmes de mesure rapides et automatiques pour l'industrie, avec la même précision que celle que nous aurions dans un laboratoire de métrologie.
Vous trouverez ci-dessous une brève comparaison pour mieux comprendre les raisons de la différence de technologies en laboratoire et dans l'environnement industriel.
Avantages de la métrologie dans l'environnement de production : mesure précise dans un environnement industriel, fiable, rapide et répétable
- mesure toutes les pièces dans un environnement industriel.
- La mesure automatique est constante dans l'évaluation.
- La mesure dans l'industrie réduit le nombre de rejets en raison du temps de latence du contrôle périodique en laboratoire.
- réduit le temps nécessaire à la mise en place des installations de production.
- Les informations de mesure peuvent être directement et en temps réel antidatées aux installations de production.
- La mesure dans un environnement industriel est plus fiable que le contrôle ponctuel.
- réduit le coût du manque de qualité.
- La mesure directe dans l'environnement de production permet un retour d'information objectif et immédiat.
- Les informations de dérive de la mesure sont utiles pour la maintenance préventive.
- augmente la qualité et la valeur du produit
- améliore l'image de l'entreprise.
Précision des laboratoires de métrologie dans l'environnement de production
TEMPÉRATURE : LTC (Compensation thermique de laboratoire)
L'une des principales causes de la perte de précision des mesures dans un environnement industriel est due à la dilatation thermique.
Par exemple, un objet de 42 mm d'aluminium a un coefficient de dilatation de 1 micron pour chaque degré centigrade. Pour obtenir une mesure correcte, il est donc nécessaire de connaître la température des instruments, de l'environnement et de chaque objet à mesurer.
Le module LTC, permet d'obtenir la même précision que celle que vous auriez dans un laboratoire de métrologie (20° ±1°) même dans des environnements de production avec une plage de température entre 10° et 60° au moyen de 4 étapes de détection.
En seulement 2 centièmes de seconde, jusqu'à 4 sources de température sont analysées et compensées.
1) la température ambiante
2) la température de la pièce
3. la température de la jauge en ligne
4) la température de l'instrument de mesure
VIBRATION : MSA (précision micro-stabilisée)
L'environnement de production n'est pas exempt de vibrations de toutes sortes, ce qui affecte considérablement la répétabilité des mesures des instruments.
En fait, une grande partie de l'instrumentation actuelle ne fournit pas d'informations sur la fiabilité de la mesure au moment où elle est effectuée, de sorte qu'en cas de vibration, il est possible qu'une mesure incorrecte soit détectée même par des instruments correctement calibrés.
Le module MSA (Micro Stabilized Accuracy) analyse le type de vibration et fournit une valeur de mesure fiable.
L'algorithme MSA qui calcule la la répétabilité en temps réel établit la mesure dans laquelle la pièce est mesurable. De cette façon, vous avez la certitude que la mesure est correcte dans l'environnement de production, ce qui est impossible avec d'autres instruments. Si une situation de mauvaise répétabilité est détectée, par exemple, la mesure peut être répétée.
IPER-RESOLUTION : XVR2 (Extended Virtual Resolution 2)
Les techniques de sous-résolution permettent d'augmenter la résolution d'une caméra, en générant une matrice de sous-pixels (dans ce cas 8 x 8) à l'aide de différentes technologies.
Grâce à l'"apprentissage profond contrôlé", des sous-pixels sont générés à partir de l'analyse des pixels adjacents sur la base de modèles pré-acquis. En métrologie, on utilise des modèles d'apprentissage particulièrement fiables, vérifiés par recoupement pour éviter de générer des informations inexactes, d'où l'expression "contrôlé l'apprentissage profond".
Une autre technologie utilisée dans ces micromètres est le "pixel shifting", les sous-pixels sont générés par l'analyse d'images séquentielles prises à différents moments et positions.
Toutes ces technologies nous permettent d'atteindre la remarquable résolution de 750 Mpixels.
EN DESSOUS DU MICRON
Lors de la mesure optique d'objets ayant une résolution inférieure au micron, nous rencontrons des problèmes liés à la longueur d'onde de la lumière. L'un d'entre eux est l'effet "speckle" qui est mis en évidence en éclairant un objet avec une source de lumière monochromatique (avec un laser, l'effet est également évident à l'œil nu).
La lumière monochromatique se reconnaît à sa couleur rouge, verte ou bleue claire.
On observe que la lumière transmise n'est pas distribuée, mais est composée de pics d'intensité sur un fond sombre. Cet effet influence encore plus la répétabilité des mesures et c'est pour cette raison que nous utilisons un éclairage polychromatique décalé particulier où les longueurs d'onde uniques qui le composent ne sont pas multiples. La lumière polychromatique décalée se reconnaît à sa coloration blanche.
Le type de matériau à mesurer, sa coloration et sa finition de surface peuvent générer de petites inexactitudes. D'où la nécessité de créer une série d'algorithmes capables de compenser cette situation.
NETTOYAGE : DAF (Dirty Advanced Filter)
Trouver des pièces propres dans l'environnement de production n'est pas une fatalité, mais est essentiel pour optimiser les mesures dans l'industrie. Le DAF (Dirty Advanced Filter) électronique permet de détecter la présence de corps étrangers solides et liquides.
Les salissures reconnues comme telles sont filtrées, ce qui améliore la précision des mesures.
Si la quantité de saleté est telle que la mesure n'est pas fiable, l'algorithme évalue la mesurabilité réelle de la pièce, ce qui peut générer un écart préventif ou une demande de mesure ultérieure après un nettoyage mécanique.
CORRECTION DE POSITIONNEMENT
Les systèmes automatiques n'ont pas toujours la possibilité de positionner les pièces avec précision, ni de réduire les temps de manipulation. Pour obtenir des mesures précises, il est donc nécessaire que le système calcule l'axe de la pièce automatiquement et précisément.
La génération des axes des pièces est configurable et permet d'adapter toutes les dimensions. Il est possible de générer plus d'un axe.
AUTO-CALIBRATION
Un instrument de mesure qui fournit des valeurs inexactes est toujours générateur de problèmes insidieux. Les systèmes de mesure dans les environnements industriels sont souvent plus sensibles aux changements de précision.
Les micromètres VEA vous permettent d'effectuer un calibrage automatique ou du moins de remarquer un calibrage incorrect. Deux modes de calibrage peuvent être choisis.
Auto-calibration en temps réel par référence placée dans le champ de vision.
Auto-calibration périodique multi-maîtres (jusqu'à 20) dans laquelle tous les paramètres de calibrage sont ajustés sur une série de maîtres de référence.
Les masters peuvent être chargés manuellement ou automatiquement.
Tests métrologiques
Nos instruments ont effectué des tests très stricts tant en laboratoire que dans un environnement industriel.
À titre de comparaison, nous avons effectué les tests en incluant et en excluant les systèmes de compensation décrits ci-dessus.
6 | 6 mm | ± 0,4 μm | ± 0,05 μm | ± 0,7 μm | ± 0,13 μm |
12 | 12 mm | ± 0,6 μm | ± 0,06 μm | ± 0,9 μm | ± 0,15 μm |
18 | 18 mm | ± 0,9 μm | ± 0,08 μm | ± 1,2 μm | ± 0,16 μm |
26 | 26 mm | ± 1,2 μm | ± 0,09 μm | ± 1,5 μm | ± 0,18 μm |
36 | 36 mm | ± 1,5 μm | ± 0,11 μm | ± 1,9 μm | ± 0,20 μm |
42 | 42 mm | ± 1,8 μm | ± 0,12 μm | ± 2,2 μm | ± 0,21 μm |
48 | 48 mm | ± 2,0 μm | ± 0,13 μm | ± 2,4 μm | ± 0,22 μm |
56 | 56 mm | ± 2,3 μm | ± 0,15 μm | ± 2,7 μm | ± 0,24 μm |
64 | 64 mm | ± 2,6 μm | ± 0,17 μm | ± 3,1 μm | ± 0,26 μm |
72 | 72 mm | ± 2,9 μm | ± 0,2 μm | ± 3,4 μm | ± 0,3 μm |
80 | 80 mm | ± 3,2 μm | ± 0,2 μm | ± 3,7 μm | ± 0,3 μm |
90 | 90 mm | ± 3,5 μm | ± 0,2 μm | ± 4,2 μm | ± 0,3 μm |
100 | 100 mm | ± 3,9 μm | ± 0,2 μm | ± 4,6 μm | ± 0,3 μm |
110 | 110 mm | ± 4,3 μm | ± 0,3 μm | ± 5,0 μm | ± 0,4 μm |
120 | 120 mm | ± 4,6 μm | ± 0,3 μm | ± 5,4 μm | ± 0,4 μm |
136 | 136 mm | ± 5,2 μm | ± 0,3 μm | ± 6,1 μm | ± 0,4 μm |
150 | 150 mm | ± 5,8 μm | ± 0,3 μm | ± 6,7 μm | ± 0,4 μm |
170 | 170 mm | ± 6,5 μm | ± 0,4 μm | ± 7,5 μm | ± 0,5 μm |
190 | 190 mm | ± 7,2 μm | ± 0,4 μm | ± 8,3 μm | ± 0,5 μm |
216 | 216 mm | ± 8,2 μm | ± 0,5 μm | ± 9,4 μm | ± 0,6 μm |
240 | 240 mm | ± 9,1 μm | ± 0,5 μm | ± 10,4 μm | ± 0,6 μm |
268 | 268 mm | ± 10,1 μm | ± 0,6 μm | ± 11,6 μm | ± 0,7 μm |
300 | 300 mm | ± 11,3 μm | ± 0,6 μm | ± 12,9 μm | ± 0,8 μm |
(1) valeur mesurée avec une échelle d'étalonnage en verre avec 25 ±2σ mesures
(2) valeur mesurée avec une prise calibrée de classe 1 de 60% à 70% du champ de vision avec 25 mesures ±2σ
GALERIE VIDÉO
les spécifications peuvent être modifiées sans préavis