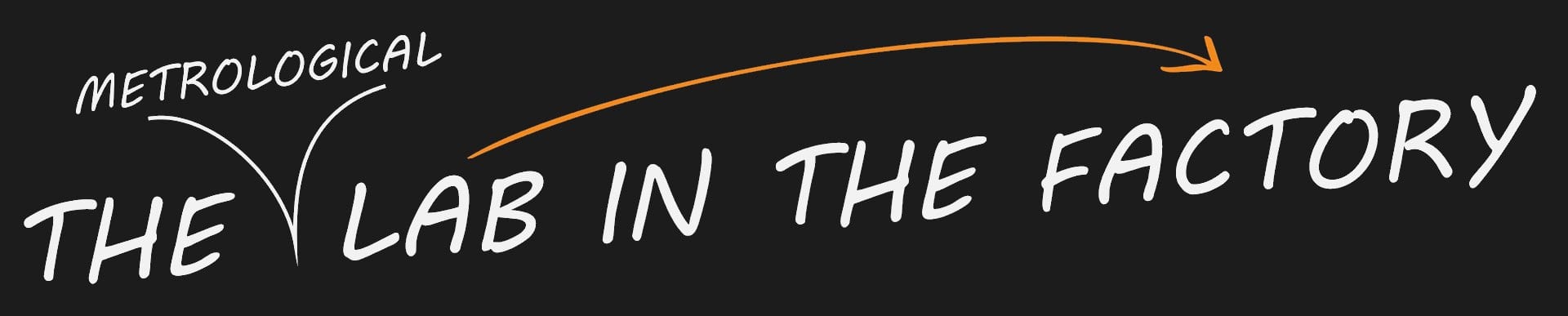
- Compensação térmica
- Estabilização da vibração
- Repetibilidade em tempo real e verificação de precisão
- Remoção digital de sujidade
- Precisão micrométrica
MEDIÇÃO PRECISA NA INDÚSTRIA: PRECISÃO DA METROLOGIA DE LABORATÓRIO NO AMBIENTE DE PRODUÇÃO
Obter uma medição precisa e rápida em um ambiente de produção é uma realidade da indústria 4.0 que torna uma empresa realmente competitiva em nível internacional.
Nos últimos anos, o controle de qualidade e a medição de 100% da produção industrial são cada vez mais necessários.
Para muitos setores industriais, há uma necessidade crescente de garantir que todos os produtos cumpram as especificações, incentivando uma migração de controle de qualidade manual para automático. A demanda por confiabilidade do produto em PPM (Parts Per Million) , torna insuficiente o controle estatístico de amostras realizado no laboratório.
Por outro lado, a aplicação prática da metrologia sempre encontrou a sua casa natural num ambiente controlado, o laboratório. A instrumentação e as tecnologias concebidas para realizar medições adaptaram-se a este ambiente, na verdade, a simples adaptação destes instrumentos ao ambiente de produção gera frequentemente problemas de fiabilidade.
Sair do laboratório e entrar diretamente na fábrica com controles rápidos e confiáveis só é possível com novas tecnologias. O principal objectivo é obter uma medição micrométrica rápida num ambiente de produção, portanto num ambiente descontrolado.
Para melhor identificar este campo tecnológico, o neologismo foi criado recentemente".Metrotronics", o resultado da união do metro(logia) e da (mecca)tronica.
O termo Metrotronics nasceu da necessidade de identificar uma série de ações, pensamentos, regras e tecnologias que representam a adaptação de instrumentos metrológicos para que possam operar direta e efetivamente em um ambiente de produção industrial.
"A LABELA METROLÓGICA NA FÁBRICA" é a filosofia por detrás deste pensamento. É necessário ser capaz de criar sistemas de medição rápidos e automáticos para a indústria, com a mesma precisão que teríamos em um laboratório de metrologia.
Abaixo está uma breve comparação para entender melhor as razões da diferença de tecnologias no laboratório e no ambiente industrial.
Vantagens da metrologia no ambiente de produção: medição precisa em um ambiente industrial, confiável, rápida e repetível
- mede todas as peças em um ambiente industrial.
- A medição automática é constante na avaliação.
- A medição na indústria reduz o número de rejeições devido ao tempo de latência da inspecção periódica no laboratório.
- reduz o tempo necessário para a instalação de instalações de produção.
- As informações de medição podem ser retroatualizadas diretamente e em tempo real para as instalações de produção.
- A medição em um ambiente industrial tem uma confiabilidade maior do que a verificação pontual.
- reduz o custo da falta de qualidade.
- medição diretamente no ambiente de produção permite um feedback objetivo e imediato.
- A informação de deriva da medida é útil para a manutenção preventiva.
- aumenta a qualidade e o valor do produto
- melhora a imagem da empresa.
Precisão laboratorial metrológica em ambiente de produção
TEMPERATURA: LTC (Compensação Térmica Laboratorial)
Uma das principais causas de perda de precisão de medição em um ambiente industrial é devido à expansão térmica.
Por exemplo, um objeto de 42 mm de alumínio tem um coeficiente de expansão de 1 mícron para cada grau centígrado, portanto, para obter uma medida correta é necessário conhecer a temperatura da instrumentação, do ambiente e de cada objeto a ser medido.
O módulo LTC, permite obter a mesma precisão que se teria num laboratório de metrologia (20° ±1°) mesmo em ambientes de produção com temperaturas entre 10° e 60° por meio de 4 etapas de detecção.
Em apenas 2 centésimos de segundo, até 4 fontes de temperatura são analisadas e compensadas.
1) a temperatura ambiente
2) a temperatura da peça
3. A temperatura do manómetro em linha
4) a temperatura do instrumento de medição
VIBRAÇÃO: MSA (Micro Precisão Estabilizada)
O ambiente de produção não está livre de vibrações de vários tipos e estas afectam significativamente a repetibilidade da medição dos instrumentos.
Na verdade, grande parte da instrumentação atual não fornece informações sobre a confiabilidade da medição no momento em que ela é realizada, portanto, em caso de vibração, é possível que uma medição incorreta seja detectada mesmo por instrumentos que estejam corretamente calibrados.
O módulo Micro Stabilized Accuracy (MSA) analisa o tipo de vibração e fornece um valor de medição confiável.
O algoritmo MSA que calcula o repetibilidade em tempo real estabelece o quão mensurável é a peça. Desta forma, você obtém a confiança de que a medição é correta no ambiente de produção, o que é impossível com outros instrumentos. Se for detectada uma situação de fraca repetibilidade, por exemplo, a medição pode ser repetida.
IPER-RESOLUÇÃO: XVR2 (Resolução Virtual Estendida 2)
As técnicas de sub-resolução permitem aumentar a resolução de uma câmera, gerando uma matriz de subpixels (neste caso 8 x 8) utilizando diferentes tecnologias.
Através de subpixels de "aprendizagem profunda controlada" são gerados a partir da análise de pixels adjacentes com base em modelos pré-adquiridos. Na metrologia, são utilizados modelos de aprendizagem particularmente confiáveis, cruzados para evitar que informações imprecisas sejam geradas, daí a expressão "controlado aprendizagem profunda".
Outra tecnologia utilizada nestes micrômetros é o "pixel shifting", os subpixels são gerados pela análise de imagens seqüenciais tiradas em diferentes momentos e posições.
Todas estas tecnologias permitem-nos alcançar a notável resolução de 750 Mpixel.
ABAIXO DO MÍCRON
Ao medir opticamente objectos com resoluções abaixo do mícron, encontramos problemas relacionados com o comprimento de onda da luz. Um deles é o efeito "mancha" que é realçado pela iluminação de um objeto com uma fonte de luz monocromática (com um laser o efeito também é evidente a olho nu).
A luz monocromática pode ser reconhecida pela sua cor vermelha clara, verde ou azul.
Observa-se que a luz transmitida não é distribuída, mas é composta de picos de intensidade sobre um fundo escuro. Este efeito influencia ainda mais a repetibilidade da medição e é por esta razão que utilizamos uma iluminação policromática particular escalonada onde os comprimentos de onda únicos de que é composta não são múltiplos. A luz policromática escalonada pode ser reconhecida pela sua coloração branca.
O tipo de material a ser medido, sua coloração e acabamento superficial podem gerar pequenas imprecisões. Daí a necessidade de criar uma série de algoritmos capazes de compensar esta situação.
LIMPEZA: DAF (Dirty Advanced Filter)
Encontrar peças limpas no ambiente de produção não é uma conclusão inevitável, mas essencial para otimizar a medição na indústria. O DAF electrónico (Dirty Advanced Filter) permite detectar a presença de corpos estranhos, tanto sólidos como líquidos.
A sujidade que é reconhecida como tal é filtrada, melhorando a precisão da medição.
Se a quantidade de sujeira for tal que a medição não seja confiável, o algoritmo avalia a mensurabilidade real da peça que pode gerar um desvio preventivo ou uma solicitação de medição posterior após a limpeza mecânica.
CORREÇÃO DE POSICIONAMENTO
Os sistemas automáticos nem sempre têm a possibilidade de posicionar as peças com precisão, também para reduzir os tempos de manuseio, portanto, para obter medições precisas é necessário que o sistema calcule o eixo da peça de forma automática e precisa.
A geração dos eixos das peças é configurável e permite a adaptação de todas as dimensões. Existe a possibilidade de gerar mais do que um eixo.
AUTO-CALIBRAÇÃO
Um instrumento de medição que fornece valores imprecisos é sempre um gerador de problemas insidiosos. Os sistemas de medição em ambientes industriais são muitas vezes mais susceptíveis a alterações na precisão.
Os micrômetros VEA permitem realizar a calibração automática ou pelo menos notar uma calibração incorreta. Dois modos de calibração podem ser escolhidos.
Auto-calibração em tempo real por referência colocada no campo de visão.
Calibração automática multi-mestre periódica (até 20), na qual todos os parâmetros de calibração são ajustados em uma série de mestres de referência.
Os mestres podem ser carregados manualmente ou automaticamente.
Testes metrológicos
Nossos instrumentos têm realizado testes muito rigorosos tanto em laboratório como em ambiente industrial.
Como comparação, realizamos os testes incluindo e excluindo os sistemas de compensação descritos acima.
6 | 6 mm | ± 0,4 μm | ± 0,05 μm | ± 0,7 μm | ± 0,13 μm |
12 | 12 mm | ± 0,6 μm | ± 0,06 μm | ± 0,9 μm | ± 0,15 μm |
18 | 18 mm | ± 0,9 μm | ± 0,08 μm | ± 1,2 μm | ± 0,16 μm |
26 | 26 mm | ± 1,2 μm | ± 0,09 μm | ± 1,5 μm | ± 0,18 μm |
36 | 36 mm | ± 1,5 μm | ± 0,11 μm | ± 1,9 μm | ± 0,20 μm |
42 | 42 mm | ± 1,8 μm | ± 0,12 μm | ± 2,2 μm | ± 0,21 μm |
48 | 48 mm | ± 2,0 μm | ± 0,13 μm | ± 2,4 μm | ± 0,22 μm |
56 | 56 mm | ± 2,3 μm | ± 0,15 μm | ± 2,7 μm | ± 0,24 μm |
64 | 64 mm | ± 2,6 μm | ± 0,17 μm | ± 3,1 μm | ± 0,26 μm |
72 | 72 mm | ± 2,9 μm | ± 0,2 μm | ± 3,4 μm | ± 0,3 μm |
80 | 80 mm | ± 3,2 μm | ± 0,2 μm | ± 3,7 μm | ± 0,3 μm |
90 | 90 mm | ± 3,5 μm | ± 0,2 μm | ± 4,2 μm | ± 0,3 μm |
100 | 100 mm | ± 3,9 μm | ± 0,2 μm | ± 4,6 μm | ± 0,3 μm |
110 | 110 mm | ± 4,3 μm | ± 0,3 μm | ± 5,0 μm | ± 0,4 μm |
120 | 120 mm | ± 4,6 μm | ± 0,3 μm | ± 5,4 μm | ± 0,4 μm |
136 | 136 mm | ± 5,2 μm | ± 0,3 μm | ± 6,1 μm | ± 0,4 μm |
150 | 150 mm | ± 5,8 μm | ± 0,3 μm | ± 6,7 μm | ± 0,4 μm |
170 | 170 mm | ± 6,5 μm | ± 0,4 μm | ± 7,5 μm | ± 0,5 μm |
190 | 190 mm | ± 7,2 μm | ± 0,4 μm | ± 8,3 μm | ± 0,5 μm |
216 | 216 mm | ± 8,2 μm | ± 0,5 μm | ± 9,4 μm | ± 0,6 μm |
240 | 240 mm | ± 9,1 μm | ± 0,5 μm | ± 10,4 μm | ± 0,6 μm |
268 | 268 mm | ± 10,1 μm | ± 0,6 μm | ± 11,6 μm | ± 0,7 μm |
300 | 300 mm | ± 11,3 μm | ± 0,6 μm | ± 12,9 μm | ± 0,8 μm |
(1) valor medido com escala de calibração de vidro com 25 ±2σ medições
(2) valor medido com ficha calibrada classe de tamanho 1 de 60% a 70% do campo de visão com 25 medições ±2σ
GALERIA DE VÍDEOS
as especificações podem mudar sem aviso prévio