La métrologie quitte le laboratoire et entre dans l'usine
Avec cet article, je vais approfondir l'un des aspects qui influencent le plus les mesures effectuées sur la chaîne de production.
Je vais faire un bref résumé pour ceux qui n'ont pas lu l'article précédent.
Dans le secteur manufacturier, notamment dans le secteur automobile, on a constaté une augmentation significative de la demande de mesures effectuées directement sur la chaîne de production.
D'où la nécessité de veiller à ce que tous les produits soient conformes au cahier des charges, ce qui rend insuffisants les contrôles statistiques par échantillonnage effectués en laboratoire.
La nécessité de sortir du laboratoire implique une série d'activités non indifférentes, tout ce qui relève de l'adaptation des instruments métrologiques pour qu'ils puissent fonctionner directement et efficacement dans un environnement de production industrielle a été identifié avec le terme "Metrotronics", un mot composé de metro(logy) e (mecha)tronic.
Parmi les différents aspects de la mesure automatique dans un environnement non contrôlé, je souligne maintenant l'aspect thermique.
La température est certainement l'un des paramètres les plus contrôlés dans un environnement de laboratoire, surtout si des mesures de longueur sont effectuées.
Habituellement, dans de nombreux laboratoires de métrologie, la température est maintenue dans une tolérance de ± 1°.
Pour avoir une référence tangible de l'incertitude générée par cette tolérance, je signale qu'un bloc d'aluminium de 42 mm pour chaque degré centigrade se dilate d'environ 1µm.
Dans un environnement de production où la température peut varier entre 15 et 35 degrés, les effets de cette incertitude sont multipliés par dix.
C'est pourquoi, pour mesurer en laboratoire une pièce de quelques kilos provenant de la production, il faut attendre qu'elle se stabilise pendant plus d'une heure (voir tableau fig.1 - temps de stabilisation - mm).
Sur la chaîne de production, cependant, la pratique la plus couramment adoptée pour réduire cette incertitude consiste à calibrer les instruments avec des échantillons de référence ayant des périodes appropriées à l'incertitude à obtenir, généralement au moins une fois par jour.
On suppose que la dilatation de l'échantillon de référence et la pièce mesurée sont égales et que l'étalonnage, ou peut-être dans ce cas, il vaut mieux dire la mise à zéro de l'instrument, permet de compenser la température ambiante.
Un des problèmes de cette pratique est que les échantillons de référence ne sont souvent pas faits du même matériau que l'échantillon mesuré, de sorte qu'ils ont des coefficients de dilatation différents, ce qui affecte négativement l'incertitude.
Il existe également des systèmes de mesure compensés en température ou, plus simplement, des tableurs qui transforment l'affichage en tenant compte de la température ambiante relevée par un thermomètre.
Ici, nous sommes toujours dans le domaine des mesures d'échantillons, mais effectuées dans un environnement de production. Cette procédure n'est peut-être pas correcte d'un point de vue formel, mais elle est encore largement utilisée, tout d'abord par les entreprises qui ne disposent pas d'un laboratoire à température contrôlée, mais aussi par les entreprises qui en ont un et qui utilisent cette procédure pour des contrôles plus fréquents.
Passons aux systèmes de mesure automatique. Que vous utilisiez des sondes LVDT (Linear Variable Displacement Transducer), des échelles optiques, des systèmes de vision optique, des lasers, ou autres, le principe ne change pas, la température fait se dilater la pièce mesurée avec tout ce que cela implique. Certains de ces instruments permettent de compenser la température, généralement la température ambiante, plus rarement celle de la pièce analysée.
La mesure de la température de la pièce semble être l'action la plus logique, mais dans la pratique, la rapidité avec laquelle les mesures sont normalement effectuées par ces systèmes automatiques ne permet pas une lecture fiable de la température.
En effet, les sondes thermiques de contact comme les thermocouples ou les Pt100 sont très lentes en raison de l'inertie thermique des matériaux dont elles sont constituées, en revanche, les sondes thermiques infrarouges (pyromètres) sont affectées, notamment pour les métaux, par le problème de l'émissivité, qui affecte leur précision.
De plus, quel que soit le type de sonde que vous utilisez, vous ne mesurerez que la surface extérieure de la pièce, et en métrotronique, cette connaissance n'est pas toujours suffisante.
Les pièces mesurées en ligne proviennent souvent de processus qui augmentent la température, plus rarement de processus qui la diminuent. Même dans des conditions de stabilité présumée, c'est-à-dire à partir de pièces provenant d'entrepôts ou de procédés qui n'affectent pas l'aspect thermique, il est souvent normal de détecter des différences de quelques degrés par rapport à la température ambiante.
Dans ces circonstances, il est facile que la température moyenne de la pièce ne corresponde pas à la température de sa surface, et encore moins à la température ambiante.
Cependant, la connaissance de la température moyenne de la pièce est nécessaire pour une mesure correcte, surtout si la précision requise est inférieure à un millième de la mesure.
Il existe probablement différentes solutions à ces problèmes, mais nous avons examiné le problème en nous concentrant sur deux aspects.
La première consiste à réaliser une sonde IR suffisamment rapide et répétable qui, à partir de la morphologie de la pièce, compense le problème de l'émissivité de manière plus efficace que le paramètre de compensation classique RTC (reflected temperature compensation).
La seconde consiste à appliquer une méthode pour connaître la température moyenne d'un objet qui se refroidit, par exemple. Pour atteindre cet objectif, nous sommes aidés par le fait que normalement les pièces mesurées dans l'environnement de production sont toujours les mêmes et que nous connaissons leurs caractéristiques.
En ayant comme données de départ certaines caractéristiques de la pièce comme le volume, la morphologie et la matière, il est possible de déterminer certains paramètres thermodynamiques comme le HTC (Heat Transfer Coefficient) et le nombre de Biot.
À partir de là, en mesurant la température de surface à différents moments de la chaîne de production, il est possible d'estimer la température moyenne au moyen de formules thermodynamiques. L'application de la loi de Fourier pour le flux de conduction dans le solide à la surface et de la loi de Newton sur le refroidissement pour la perte par convection à la surface, permet d'obtenir des résultats déjà discrets ; des formules plus complexes permettent une meilleure fiabilité.
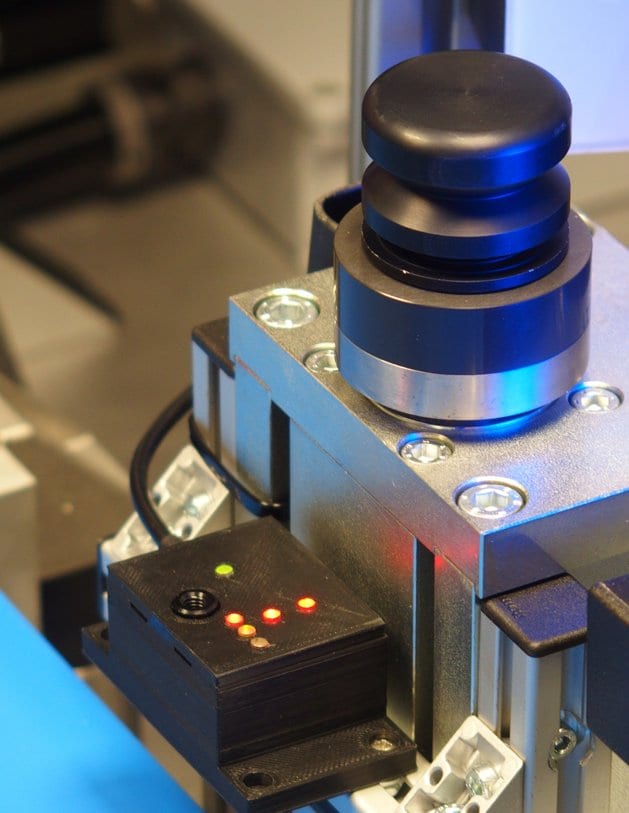
Le résultat de ces deux recherches sont les nouveaux capteurs thermiques, particulièrement compacts, de la série HCE-TMP, qui sont spécialement conçus pour compenser thermiquement les systèmes de mesure en production.