La metrologia esce dal laboratorio ed entra in fabbrica
Con questo articolo approfondirò uno degli aspetti che più influenza le misure effettuate in linea di produzione.
Faccio un breve riassunto per chi non avesse letto l’articolo precedente.
Nel comparto manifatturiero, soprattutto in quello legato all’automobile, si è registrato un notevole incremento nella richiesta di misure eseguite direttamente in linea di produzione.
Da qui nasce l’esigenza di garantire che la totalità dei prodotti sia conforme alle specifiche, rendendo così insufficiente il controllo statistico a campione effettuato in laboratorio.
La necessità di uscire dal laboratorio comporta una serie di attività non indifferenti, tutto ciò che rientra nell’ambito dell’adattamento degli strumenti metrologici in modo che possano operare direttamente ed efficacemente in un ambiente di produzione industriale è stato identificato con il termine “metrotronica”, parola composta di metro(logia) e (mecca)tronica.
Tra i vari aspetti della misurazione automatica in ambiente non controllato evidenzio ora l’aspetto termico.
La temperatura è sicuramente uno dei parametri più controllati in un ambiente di laboratorio, soprattutto se vengono eseguite misure di lunghezze.
Solitamente in parecchi laboratori metrologici la temperatura è mantenuta entro una tolleranza di ± 1°.
Per avere un riferimento tangibile dell’incertezza generata da questa tolleranza faccio presente che un blocco di alluminio di 42 mm per ogni grado centigrado si dilata di circa 1µm.
In ambiente di produzione dove la temperatura può variare anche tra i 15 e i 35 gradi gli effetti di questa incertezza vengono decuplicati.
Per questa ragione per misurare in laboratorio un pezzo di qualche Kg proveniente dalla produzione bisogna attendere che si stabilizzi anche per più di un’ora (vedi tabella fig.1 tempi-stabilizzazione-cmm).
In linea di produzione invece la prassi che viene più comunemente adottata per ridurre questa incertezza è quella di calibrare gli strumenti con dei campioni di riferimento con periodi adeguati all’incertezza che si vuole ottenere, solitamente almeno una volta al giorno.
Si presume infatti che la dilatazione del campione di riferimento e del pezzo misurato siano uguali e la calibrazione o forse in questo caso è meglio dire l’azzeramento dello strumento, permette di compensare la temperatura ambiente.
Uno dei problemi di questa prassi è che i campioni di riferimento spesso non sono dello stesso materiale del misurato, per cui hanno coefficienti di dilatazione differenti e questo incide negativamente sull’incertezza.
Esistono anche sistemi di misura compensati in temperatura o più semplicemente fogli elettronici di calcolo che trasformano il dato letto tenendo conto della temperatura ambiente presa da un termometro.
Qui siamo ancora nel campo della misurazione a campione, effettuata però in ambiente di produzione. Si tratta di una procedura forse non corretta dal punto di vista formale, ma ancora molto utilizzata in primis da aziende che non dispongono di un laboratorio a temperatura controllata, ma anche da aziende che ce l’hanno e che usano questa procedura per i controlli a maggior frequenza.
Passiamo ora ai sistemi di misura automatica. Che si usino sonde LVDT (Linear Variable Displacement Transducer), righe ottiche, sistemi ottici di visione, laser, od altro ancora, il principio non cambia, la temperatura fa comunque dilatare il pezzo misurato con tutto ciò che ne consegue. Alcuni di questi strumenti permettono la compensazione della temperatura, solitamente quella ambiente, più raramente quella del pezzo analizzato.
Misurare la temperatura del pezzo sembrerebbe l’azione più logica, in pratica però la velocità con cui normalmente vengono effettuate le misure da questi impianti automatici, non permette di fatto una lettura affidabile della temperatura.
Infatti le sonde termiche di tipo a contatto come le termocoppie o le Pt100 sono molto lente a causa dall’inerzia termica dei materiali da cui sono costituite, di contro le sonde termiche ad infrarossi (pirometri) risentono, soprattutto per i metalli, del problema dell’emissività, che ne inficia la precisione.
Inoltre, qualunque tipo di sonda si usi, si misurerà solo la superficie esterna del pezzo, ed in metrotronica questa conoscenza non è sempre sufficiente.
I pezzi misurati in linea spesso provengono da processi che ne innalzano la temperatura, più raramente da processi che l’abbassano. Anche in condizioni di presunta stabilità, ossia da pezzi che provengono da magazzini o da lavorazioni che non influiscono sull’aspetto termico, spesso è normale rilevare differenze di qualche grado rispetto la temperatura ambiente.
In queste circostanze è facile che la temperatura media del pezzo non corrisponda alla temperatura della sua superficie e tantomeno alla temperatura ambiente.
La conoscenza della temperatura media del pezzo risulta però necessaria per una corretta misurazione, soprattutto se l’accuratezza richiesta è inferiore a un millesimo della misura.
Probabilmente esistono soluzioni diverse a queste problematiche, dal nostro canto abbiamo esaminato il problema focalizzandoci su due aspetti.
Il primo è realizzare una sonda IR sufficientemente veloce e ripetibile che, partendo dalla morfologia del pezzo, compensi il problema dell’emissività in un modo più efficace rispetto al classico parametro di compensazione RTC (reflected temperature compensation).
Il secondo è applicare un metodo per conoscere la temperatura media di un oggetto che si sta, ad esempio, raffreddando. Per raggiungere questo obiettivo ci viene in aiuto il fatto che normalmente i pezzi misurati in ambiente di produzione sono sempre gli stessi e ne conosciamo le caratteristiche.
Avendo come dati di partenza alcune caratteristiche del pezzo quali il volume, la morfologia ed il materiale è possibile determinare alcuni parametri di termodinamica come HTC (Heat Transfer Coefficient) e il numero di Biot.
Da qui, misurando la temperatura superficiale in tempi diversi sulla linea di produzione è possibile stimare la temperatura media tramite formule di termodinamica. L’applicazione della legge di Fourier per il flusso di conduzione nel solido in superficie e la legge di raffreddamento di Newton per la perdita convettiva in superficie, permettono di ottenere già discreti risultati; formule più complesse permettono una migliore attendibilità.
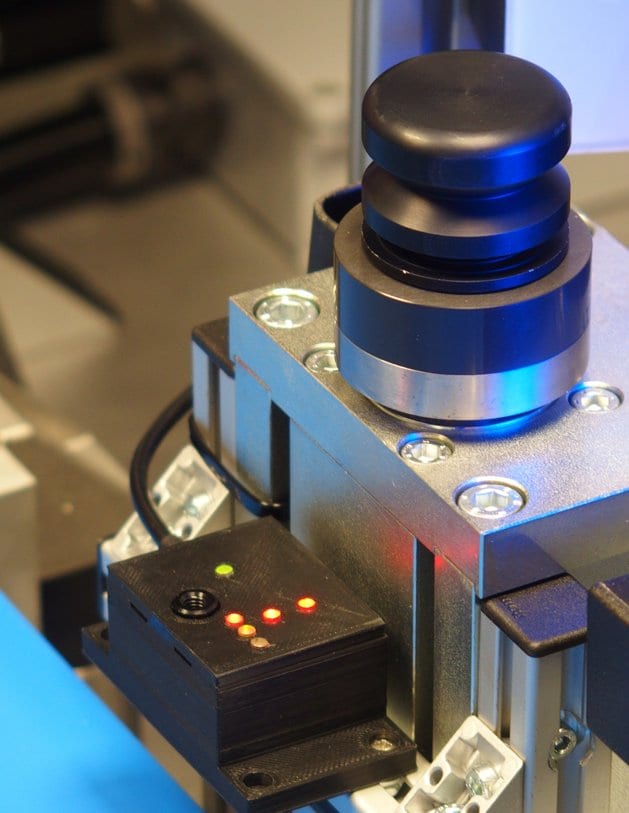
Il risultato di queste due ricerche sono i nuovi sensori termici particolarmente compatti della serie HCE-TMP espressamente progettati per compensare termicamente i sistemi di misura in produzione.